Metallurgy
Predict Product Performance
Metallurgical testing helps you predict the future, so you can prevent failure and strengthen results.
Metallurgy is the science and study of metals. Through testing and characterizing a metal’s microstructure, chemical and mechanical properties, we can determine whether it is suitable for a particular application or conforms to a required drawing or specification.
Metallurgical analysis can be employed as part of a quality assurance program and has many applications in research and development.
We offer metallurgical testing as a stand-alone service or as a complement to any of our non-destructive testing services. Our metallurgical lab is accredited by A2LA for ISO/IEC 17025; AS9100 and is certified as a General Electric S-400 facility.
American Testing Services will provide you with a high quality, reliable solution to your metallurgical needs. Whether it is failure investigation, routine chemical and mechanical testing, or material selection, our skilled metallurgists can guide you along the most cost-effective path to find the answers you need.
Our Metallurgy Testing Capabilities
Chemical Testing
American Testing Services provides a range of destructive and non-destructive methods in determining unknown material or conformance to specifications and drawings. Contact our metallurgical department for more information or help in determining the proper method/technique needed for evaluation of your material.
Destructive
Combustion Analysis (Carbon and Sulfur)
We provide precise carbon and sulfur quantification of metallic samples by combustion evaluation. A sample size of 1 gram minimum is necessary for proper testing using this method.
Optical Emission Spectroscopy (Glow Discharge OES)
Rapid evaluation of the full composition of metallic samples is available through GDS analysis. This can be conducted on a wide range of alloys, in evaluation of unknown samples or in determining conformance to specifications.
Inductively Coupled Plasma – Optical Emission Spectrometry (ICP-OES)
ATS offers evaluation of trace elements as well as major elemental composition by ICP-OES. This fully destructive chemical analysis is typically used on samples too small for GD-OES, or for trace analysis. Inductively coupled Optical Emission inspection utilizes a very hot plasma arc (>10,000 degrees F) to ionize a liquid sample and break it down for analysis.
Non-destructive
Positive Material Identification (X-Ray Fluorescence Analysis)
ATS can provide rapid non-destructive qualitative chemical evaluation of material and/or finished machined parts, both in-house, and on-site at the customer’s location by the use of a portable Positive Material Identification (PMI) analyzer. This rapid testing method can be used for material sorting, confirming correct use of alloy, or in identifying unknown material.
Energy Dispersive X-ray Spectrometry (Via Scanning Electron Microscope)
For the evaluation of debris/contamination, evaluation of plating, analysis of microstructural phases or for small samples, qualitative and semi-quantitative analysis by energy dispersive x-ray analysis is available. Energy Dispersive Spectroscopy (EDS) is used in conjunction with examination using Scanning Electron Microscopy (SEM) at magnifications ranging from 20 to 20,000X. ATS features Variable Pressure Scanning Electron Microscopy (VPSEM) services. Using the SEM in the VPSEM mode at high pressure and low vacuum, allows for the examination and analysis of nonconductive materials without the need for sputter coating with gold or carbon. The VPSEM mode produces high resolution imagery with good depth of field using secondary and backscattered electron collection and processing.
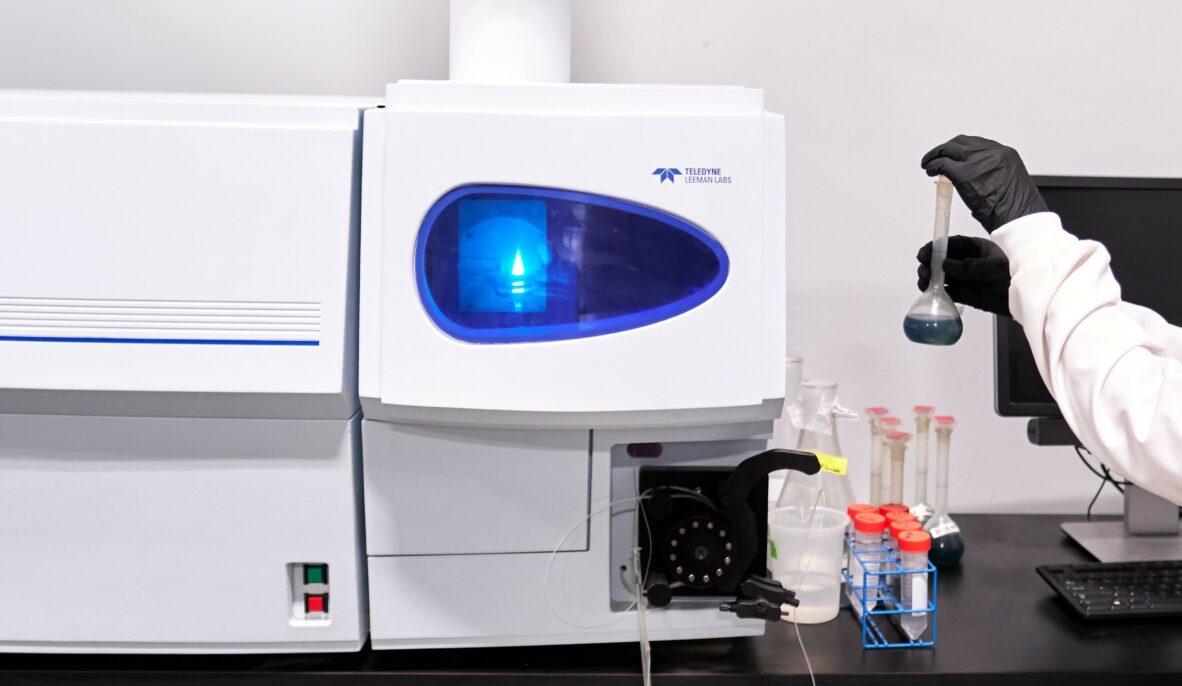
Corrosion Testing
Parts produced from material which has been improperly heat treated may fail prematurely in service through intergranular attack, pitting or cracking. In order to insure the proper processing of many grades of stainless steel, ATS offers corrosion screening and testing in accordance with widely recognized ASTM standard A262. Pitting and crevice corrosion resistance of some grades is sometimes evaluated using the Ferric Chloride immersion test specified in ASTM G48.
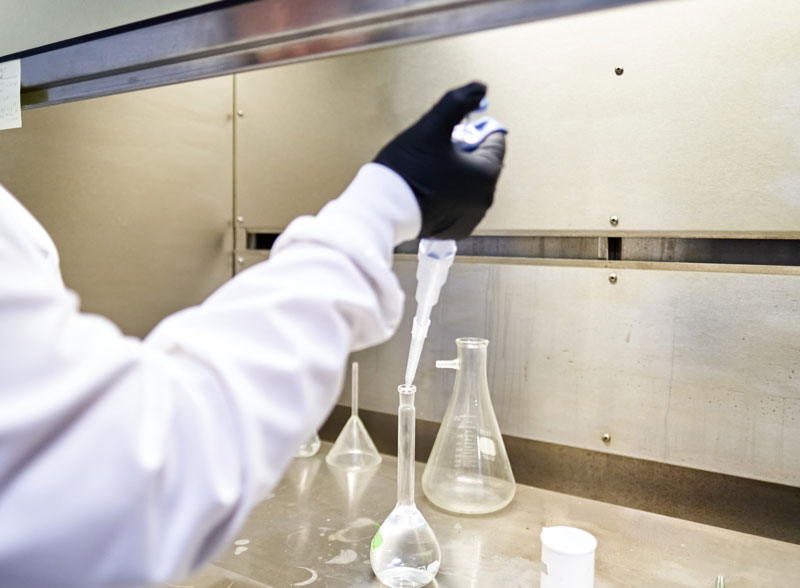
Failure Analysis
Determining why metal components and assemblies fail is one of the most important aspects of metallurgical testing and inspection. Through use of all available laboratory tools and techniques, we can determine the root cause of the failure and make recommendations in material selection and processing to prevent the recurrence of future problems. ATS’s highly qualified staff of Metallurgists boast many years of experience in failure investigation support to the aerospace, US Department of Defense weapons programs, automotive and commercial sectors.
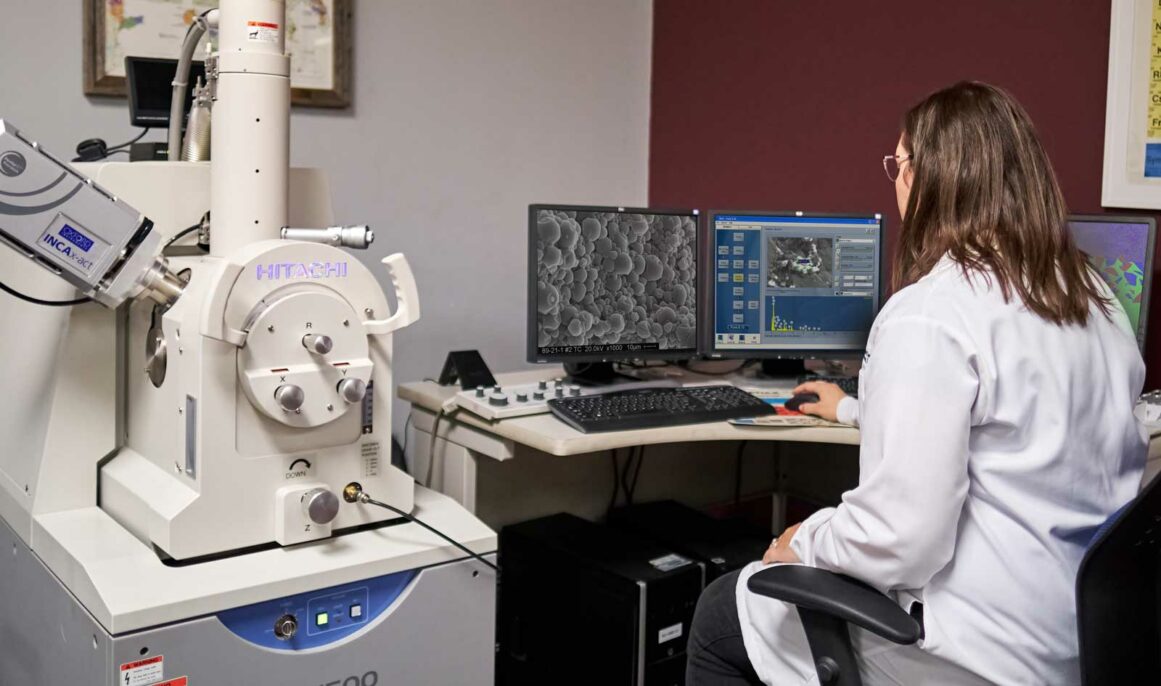
Mechanical Testing
Charpy Impact Testing
This testing is conducted by striking a precisely machined notched specimen with a swinging hammer and measuring the energy the sample absorbed during the impact. This determines the notch sensitivity and impact toughness of material at a range of temperatures. Ductile to brittle transition temperature can be determined by evaluating and comparing impact energy at temperatures ranging from room temperature to minus 321 degrees Fahrenheit, which is important when designing components to be used in a variety of environments.
Tensile testing
Sample preparation and tensile testing are generally conducted in accordance with standard ASTM practice such as ASTM A370, E8 and ASTM B557. Tensile tests are used to determine the modulus of elasticity, elastic limit, elongation, proportional limit, reduction in area, tensile strength, yield point, yield strength and other related properties.
Hardness
Indentation hardness testing is a time-tested method of judging the relative hardness of a variety of metal, their alloys and of polymers. These test methods include Macro Vickers, Micro Vickers, Knoop Microhardness, Standard Rockwell, Superficial Rockwell, Brinell Hardness testing and Durometer. Since measured hardness levels are often directly correlated to measured tensile properties, hardness testing provides a quick and effective measure of target properties achieved through various types of processing, such as heat treatment or cold working.
Proof Load Testing
Brazed, welded and machined assemblies and components can be fixtured, secured in one of our Universal Testing machines and loaded in either tension or compression to a prescribed or design proof load. Following visual examination for deformation, cracking or breakage the part may be further evaluated by one of several comprehensive non-destructive examination disciplines such as magnetic particle inspection, fluorescent penetrant inspection, ultrasonic inspection or radiography.
Bend Testing
Acceptance testing, or requalification testing, of some materials requires that the ductility and surface integrity of the material be tested by wrapping, or bending, a sample around a specified mandrel size. This is commonly seen in Aerospace Material Specifications (AMS) for some stainless steels and high alloy materials.
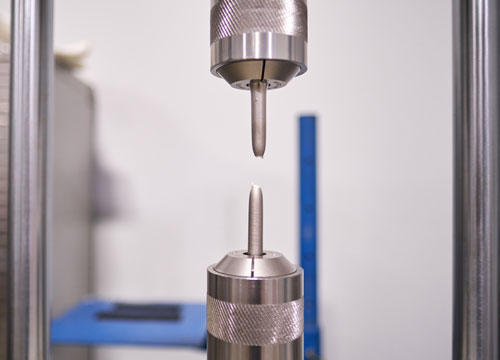
Metallography
Metallography is the study of the structure of materials using microscopy. Metallography is a fascinating science, in that all metals have a microstructure unique to themselves, depending upon how they have been processed and heat treated. By microscopic examination of the structure, both as-polished and etched, with a suitable base or acid solution, we can determine the grade and heat-treated condition, grain size, inclusion content, microconstituents and phase distribution. The changes in steel microstructures through various heat treatments was first documented over 150 years ago. Metallography is an invaluable tool to the metallurgist in determining the general quality of wrought, cast and additive manufactured metal produced regarding features such as micro cleanliness, chemical segregation, carburization, decarburization, intergranular oxidation, alloy depletion and eutectic melting. It is therefore an indispensable tool in failure investigations and quality control screenings.
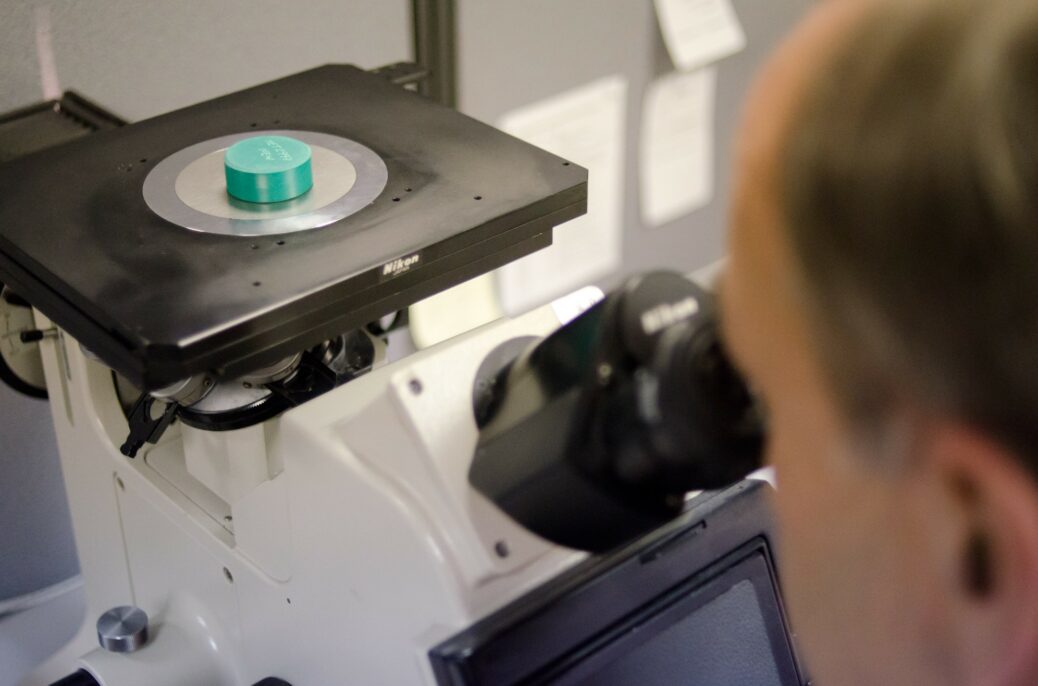
Weld Qualification Testing
ATS offers weld and brazing procedure and performance qualification testing to clients for accredited certification to a number of US, European and Asian codes. Testing may include macro sections, micro sections, macro and micro hardness surveys, face bends, root bends, side bends, reduced section tensile testing, all weld metal tensile testing, charpy impact testing, ultrasonic inspection, penetrant inspection, visual inspection, magnetic particle inspection and radiography.
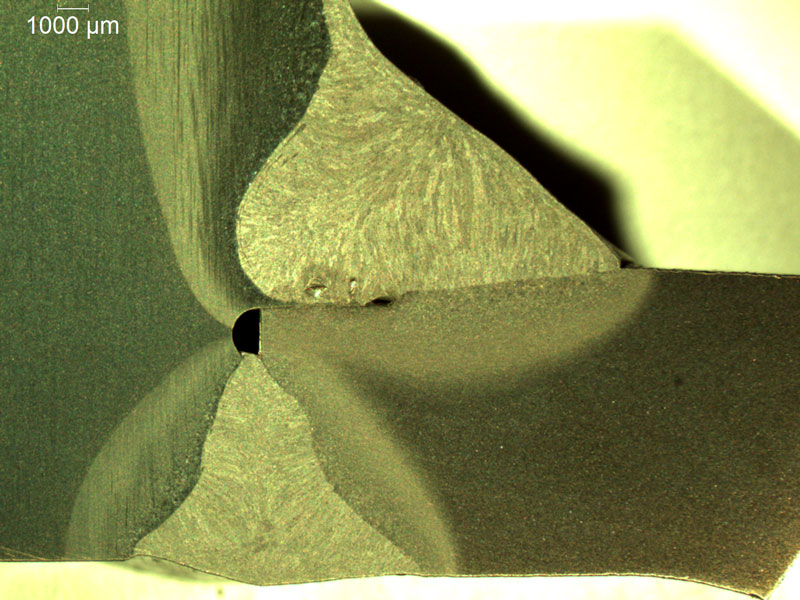
Metallurgy vs. Non-Destructive Testing
Metallurgy breaks it so you know how, why and where it’s possible to fail. NDT shows you what you need to see without breaking it. Arm yourself with the knowledge you need to know, before you need to know it.
Metallurgy & NDT Solutions That Provide You With Peace of Mind
In addition to metallugical and non-destructive testing, ATS offers a full range of complementary services to keep your business running such as training, equipment calibrations and consulting.
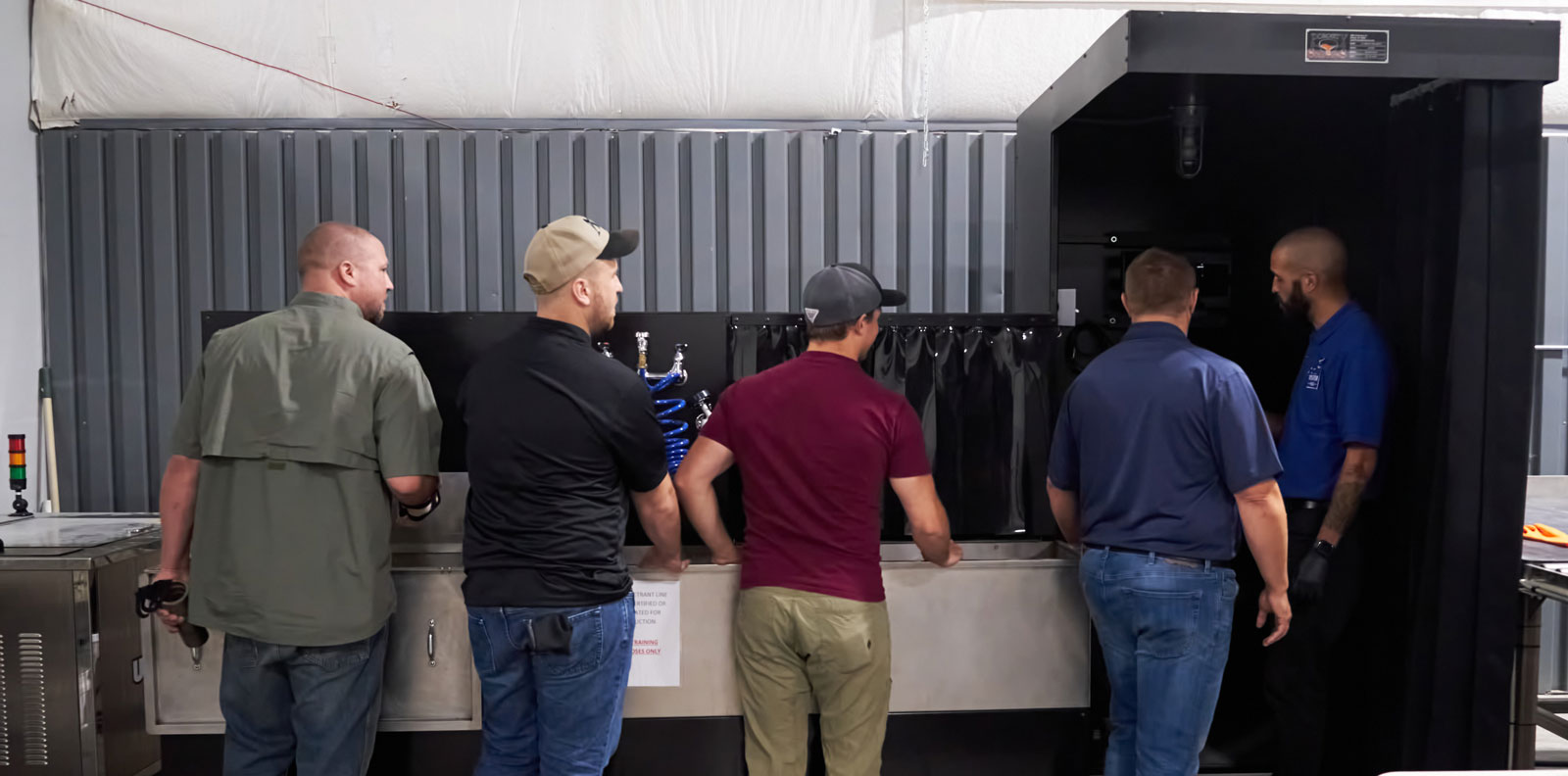
Training

Equipment Calibrations
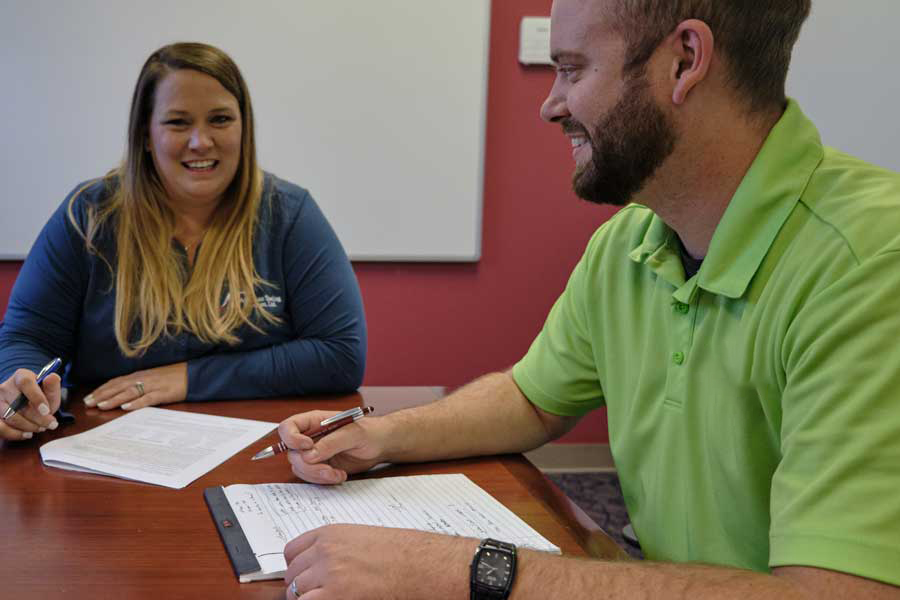